Amorphous Alloys
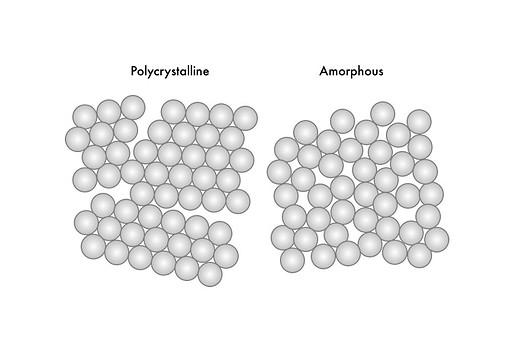
Over the years you may have heard of Liquidmetal®, VitreloyTM, Metallic Glass & Bulk Metallic Glasses, all virtually synonymous with Amorphous Alloys. Today, alongside improvements in production capabilities, these alloys have come of age.
Amorphous alloys, though metallic, solidify like glass. Owing to their disordered atomic structure (like that of glass) metallic glasses usually exhibit many exceptional properties which include higher strength sometimes near theoretical limits (over 5 Giga Pascal) and carbide-like hardness, superior strength-to-weight ratio, as well as better corrosion and wear resistance compared to polycrystalline metals of similar alloy compositions. And unlike regular glass or ceramics - they are tough!
While each amorphous alloy formulation is unique, most are Zirconium based. Four alloying elements are required at a minimum, and Zirconium is of particular suitability due to its glass-forming ability, deep eutectic point (enabling alloying with a number of other metals) and corrosion resistance. Other metals typically used are: Titanium, Niobium, Nickel, Palladium, Aluminium, Iron, Beryllium and Copper.
Amorphous alloys are of particular interest in manufacturing these days, for the reason that they can be processed to near net shape, with little shrinkage. In the bid to reduce production time, cost and waste while increasing output, amorphous alloy components have found their niche. Production via casting, injection moulding, 3D printing/ additive manufacturing adds further characteristics to each unique formulation and application within the following industries: jewellery/watchmaking, electronics, automotive, medical/dental, space & sports gear. An exciting, major growth area is in applications related to 5G technologies and infrastructure.
​
As a minor metals trading company, we supply Zirconium, which is often a key constituent of amorphous alloys.