How the addition of Gold led to a new harder Titanium alloy with potential for use in implants
- Lipmann Walton & Co Ltd
- Sep 20, 2016
- 3 min read
Updated: Aug 10, 2023
By Harry Sherwood
A few months ago, my brother was playing football when he landed at an odd angle and broke his ankle really badly.
Known as a Trimalleolar Fracture, the break parted all three of the bones that join foot and leg and is notoriously challenging to fully recover from, with a large proportion of people not being able to play sport to the same quality again. Soon my brother found himself in hospital, surgeons measuredly scheming their immanent repair job: with nothing connecting his foot to the rest of his body, it was going to be a tough one.

The plates used need to be both incredibly strong and sufficiently light. Early orthopedic plates (first used at the turn of the last century) were made from steel or iron. Later plates were shaped in such a way as to make them stronger, but they still faced a very crucial enemy: corrosion. Submerged in conditions comparable to warm, highly oxygenated seawater, an electrochemical reaction takes place where metal ions are removed from the implant and leeched into the surrounding blood. Over time, the strength of the device is compromised. Orthopaedic plates after the 50s and 60s were reformulated from stainless steel, which was far more corrosion-resistant, but still quite heavy.
But around a decade before this, an important discovery (by Bothe et al) had gone largely unreported. Having screwed small titanium cylindrical implants into rabbit femurs, they noticed ‘osteogenesis’ after only 3 days: the bone was growing around the titanium, lassoing it with woven fibres and accepting it as its own. After a few weeks, the researchers attached tension springs to the implanted pegs and discovered, amazingly, that the pegs were not just superficially encapsulated by the rabbit bone, but were structurally bonded to it.
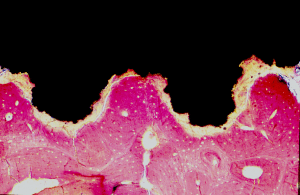
It took thirty years for this ‘osseointegration’ to be accepted by the scientific community in all fields where it could be used (eg. dentistry). The founder of this movement, a Swede named Brånemark, reportedly encountered many years of resistance while promoting the technique, and even at one point had his research funding pulled. Nevertheless, by the 80’s scientists had come round to the idea of titanium biocompatibility.
Nowadays, titanium is still the go-to metal for implants of many types – but could this be about to change? A recent (July 2016) paper seems to show that Titanium might not be the ultimate metal after all – or at least not alone.

The team of scientists working at Rice University used an high-powered arc in order to melt together titanium and gold together in specific ratios. As discussed earlier, strength & corrosion resistance are obviously essential for implants and plates, but in certain implants (for instance knee replacements) the fixtures must also be very resistant to wear because they are designed to rub against each other for much of the day. This isn’t the first time that titanium and gold have been alloyed, but previous attempts have yielded materials with comparatively disappointing hardness values. This time, the alloy created was around four times harder than titanium.
The secret to this fourfold increase lies in the structure of the alloy, in which gold and titanium atoms nestle in a three-dimensional bonding-network of cubic structure. The alloy isn’t an ionic compound, as both elements are metallic. However, it does show ionic character in the sense that the atoms experience forces of attraction to each other. This arrangement reduces the distance between the atoms, increasing the forces of attraction and the resulting strength and hardness of the alloy.
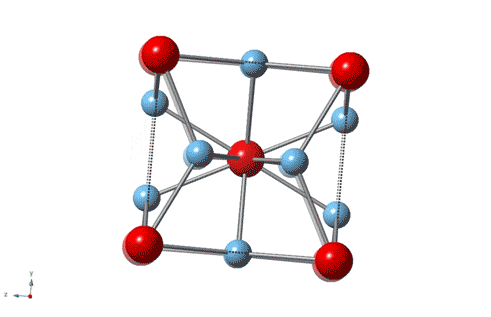
This is obviously very exciting news – but not only in the world of implants. Other applications, for example in engineering, are not far away. The only drawback of this alloy seems to be the cost: with ¼ of the material pure gold, 100g of the stuff would cost around £750 – and that’s before it is engineered into anything usable. Since this combination had been tried before without drastic increases in strength, it seems that what is needed is for scientists to revisit other alloying metals, such as tin, aluminum and cobalt in the hopes of achieving different metallic arrangements.
By courtesy of Harry Sherwood
Comments